A Comprehensive Overview of Storage Tank Welding Inspection Specifications and Methodologies for Improved Weld Quality and Performance
The value of welding evaluation criteria in the production of tanks can not be overstated, as they act as the backbone for making certain weld integrity and operational integrity. Various assessment techniques, including visual analyses and progressed non-destructive testing approaches, are crucial in recognizing potential imperfections that might compromise performance. Moreover, sticking to regulatory standards not only enhances weld quality however additionally alleviates the threat of expensive failings. As we check out the nuances of these approaches, it comes to be necessary to take into consideration just how a systematic technique can revolutionize current methods and bring about substantial enhancements in end results.
Relevance of Welding Evaluation Criteria
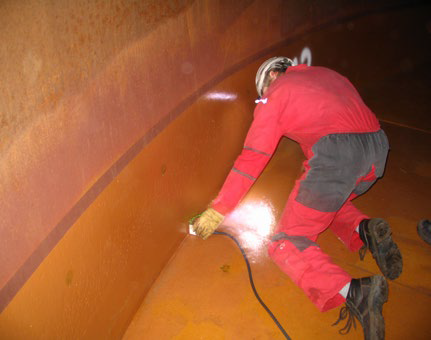
Welding examination criteria include a variety of requirements, consisting of material specifications, welding treatments, and certifications of personnel associated with the welding procedure. By imposing these requirements, organizations can systematically determine and remedy prospective issues, thus minimizing the possibility of costly repair services or catastrophic failings. Moreover, extensive inspection techniques foster a society of responsibility and accuracy, urging welders to keep high degrees of craftsmanship.
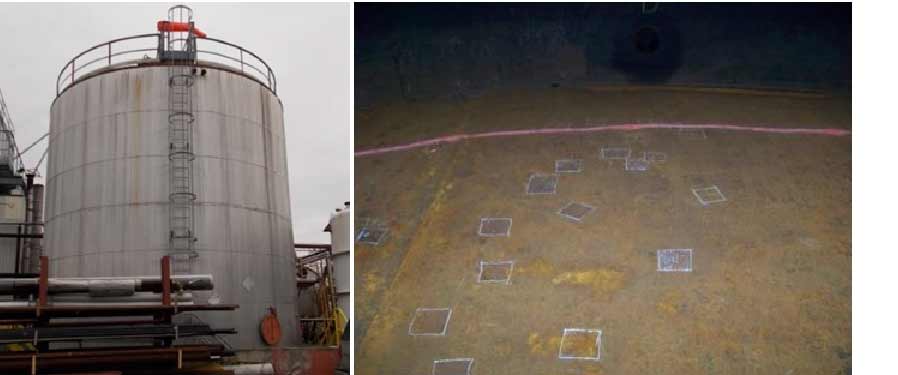
Common Welding Inspection Techniques
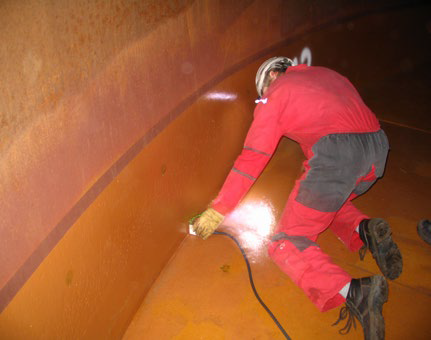

Ultrasonic Checking (UT) is one more common method, utilizing high-frequency sound waves to identify inner problems that may not be noticeable externally. This method is particularly effective for determining voids or inclusions within the weld steel. Magnetic Bit Evaluating (MT) is also widely made use of, particularly for ferromagnetic materials, as it exposes surface and near-surface flaws through the application of magnetic fields and ferrous fragments.
In Addition, Fluid Penetrant Testing (PT) spots surface-breaking defects by using a penetrant to the weld and after that using click a programmer to extract the penetrant. Each of these techniques adds to a detailed evaluation strategy, making sure that welds satisfy the strict top quality standards required in storage tank building and construction.
Governing Standards and Compliance
Regulative requirements and conformity are crucial elements in making sure the safety and dependability of bonded structures in container building and construction - Tank Welding Inspection. These requirements serve to develop minimum demands for material residential or commercial properties, welding procedures, and evaluation practices, consequently reducing the danger of structural failings and boosting total efficiency
Trick organizations, such as the American Society of Mechanical Designers (ASME) and the American Welding Society (AWS), give guidelines that are widely embraced in the market. Compliance with these standards not just ensures adherence to ideal practices yet also fulfills legal and legal obligations, protecting the interests of stakeholders.
Regulatory bodies frequently mandate adherence to details codes, such as ASME Code Section IX for welding qualifications and API 650 for bonded containers. These codes detail demands for welding techniques, qualifications of personnel, and testing methods to validate weld stability.
Normal audits and inspections are critical to preserving compliance, as they aid identify deviations from developed requirements. Non-compliance can result in substantial charges, task hold-ups, and safety risks. Hence, a robust understanding of regulative criteria and a dedication to conformity are critical in accomplishing high-grade and durable welded container structures.
Non-Destructive Examining Approaches
Just how can the honesty of bonded structures be guaranteed without causing damage? Non-destructive screening (NDT) approaches use a durable option, making it possible for inspectors to assess weld quality without compromising the product - Tank Welding Inspection. Among one of the most usual NDT methods are ultrasonic screening (UT), radiographic screening (RT), magnetic bit testing (MT), and color penetrant testing (PT)
Radiographic testing involves passing X-rays or gamma rays via the weld, creating photos that disclose structural defects such as splits or spaces. This approach is invaluable for analyzing the stability of complex welds.
Magnetic fragment screening is suited for ferromagnetic materials, where magnetic fields disclose surface and near-surface gaps. Color penetrant testing makes use of a liquid dye to highlight surface-breaking imperfections, making it an efficient approach for non-porous materials.
Each of these NDT approaches has distinct benefits, enabling detailed evaluations tailored to certain materials and welding processes. By applying these strategies, markets can make sure the dependability and safety of welded frameworks, ultimately improving total efficiency.
Enhancing Weld Quality Through Examination
Effective assessment plays an essential role in improving weld quality, serving as an essential checkpoint in the fabrication procedure. By determining potential problems early, examinations minimize the risk of compromised architectural integrity and guarantee conformity with sector standards. Employing this link a combination of aesthetic examinations, non-destructive testing (NDT) approaches, and mechanical analyses, assessors can discover issues such as porosity, splits, and incomplete combination.
Applying a durable inspection protocol not only boosts the total quality of welds yet also fosters a culture of responsibility amongst welders and producers. Normal training and qualification of examination employees make certain that they are equipped with the necessary skills to recognize and resolve possible troubles properly. This aggressive technique lessens rework and connected expenses, eventually adding to project efficiency.
Furthermore, thorough documents of assessment searchings for gives important understandings right into recurring issues, assisting in continual renovation in welding methods. By leveraging advanced technologies, such as automated ultrasonic testing or electronic radiography, weld high quality can be enhanced via a lot more exact assessments. In verdict, an extensive assessment procedure is crucial in achieving top quality welds, guaranteeing security, reliability, and durability in tank manufacture.
Final Thought
In verdict, the implementation of extensive storage tank welding evaluation requirements and techniques is vital recommended you read for making certain weld integrity and performance. By utilizing a combination of visual assessments, non-destructive testing techniques, and adherence to regulative criteria, companies can properly identify and reduce prospective issues.
Comments on “Tank Welding Inspection: Ensuring Long-Term Durability and Security”